Tina Dardeno ’14 Aims to Prevent Bone Fractures during Implantation

11/01/2016
By Edwin L. Aguirre
The femur, or thighbone, is the longest and strongest of the body’s more than 200 bones. It is attached to the hip bone with a smooth, cartilage-lined ball-and-socket joint. The joint carries not only the full weight of a person’s body, but it can also withstand the pressure and impact of walking, running and jumping as well as lifting heavy loads.
Over time, the cushioning layer of cartilage gets worn out or damaged due to age, arthritis or traumatic injury, oftentimes requiring the joint to be replaced surgically with an artificial implant made of metal alloy and polyethylene plastic or ceramic. During total hip replacement, also called total hip arthroplasty, it’s difficult for surgeons to gauge how much pressure to apply to seat the implant. Too little pressure, and it may not properly attach; too much, and it may fracture the femur.
Mechanical engineering Ph.D. student Tina Dardeno ’14 intends to make the process less of a guessing game. The National Science Foundation (NSF) — which recently awarded her a prestigious Graduate Research Fellowship Award — believes she can do it.
“When a young, active or heavy person requires hip replacement, the orthopedic surgeon typically chooses ‘cementless’ implant technology, which is stronger and allows the patient’s natural bone to grow directly onto the prosthesis without using any adhesive,” says Dardeno, who is a graduate research assistant at the university’s Structural Dynamics and Acoustic Systems Laboratory (SDASL). “After sawing off the femur’s head, the surgeon uses a special tool to widen the femoral canal just enough so that the implant’s long, pointed stem can be tightly fitted into the canal.”
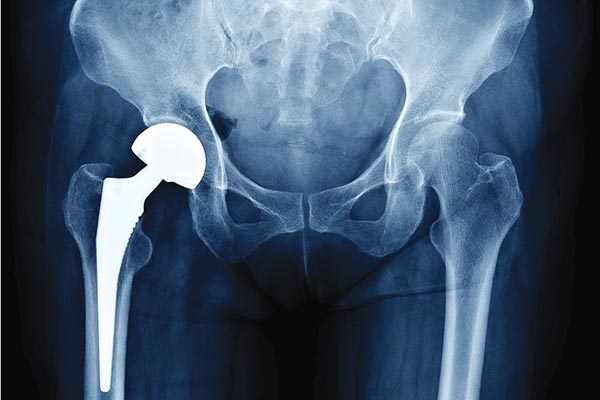
Currently, no method exists that can accurately assess the implant’s stability during the operation. “Surgeons must rely solely on their clinical experience to determine the right amount of pressure to apply to properly seat the implant,” says Dardeno.
In response, she is currently developing a non-contact, non-invasive method for monitoring the insertion and seating of cementless femoral implants in real-time. Using an implant and full-size femur replicas, she will conduct analytical modeling and vibration analysis of the femoral areas that will normally be exposed during surgery. She will measure the strain on the implant’s head using digital image correlation, an optical technique that employs multiple, high-resolution video cameras to create precise 3-D measurements of a material’s deformation, vibration and stress. Dardeno plans to expand her modeling to encompass not only the head but the entire length of the implant.
“My goal is to characterize the distribution of strain throughout the implant,” she says. “The resulting full contour map can potentially be used to predict the location and severity of fractures during insertion of the femoral implant.”
Dardeno transferred to UMass Lowell in the fall of 2011, after completing a bachelor’s degree in nursing (summa cum laude) at Northeastern University and passing the board exam in 2010. She earned a bachelor’s degree in mechanical engineering (summa cum laude) from UMass Lowell in 2014. “My education and experience as a nurse and engineer make me uniquely qualified to pursue this research,” she says.
An NSF Graduate Research Fellow
According to the NSF, the Graduate Research Fellowship Program supports outstanding graduate students “who can contribute significantly to research, teaching and innovations in science and engineering. These individuals are crucial to maintaining and advancing the nation’s technological infrastructure and national security as well as contributing to the economic well-being of society at large.”
“Tina’s research clearly demonstrates her ability to bridge engineering with the medical field and address a very important issue that has both technical and societal benefits,” says mechanical engineering Prof. Peter Avitabile, who is director of SDASL and Dardeno’s thesis adviser.
Dardeno will receive from the NSF a three-year, annual stipend of $34,000, along with a $12,000 cost-of-education allowance for tuition and fees (paid to UMass Lowell) and opportunities for international research and professional development.
Earlier in her academic career, Dardeno spent six months as research co-op student in an endocrinology lab at Beth Israel Deaconess Medical Center in Boston and also held a summer internship at Instrumentation Laboratory in Bedford, Mass. In 2014, she was awarded the Dean’s Gold Medal for highest achievement in mechanical engineering as an undergraduate. To date, she has two papers published in peer-reviewed journals as well as several conference papers.
“My experiences working in the SDASL will surely be invaluable to my career,” says Dardeno. “They provide the foundation and hands-on research training I need beyond the classroom. Having faculty mentors who emphasize both experimental and analytical structural dynamics and acoustics has given me a very complete and well-rounded education.”