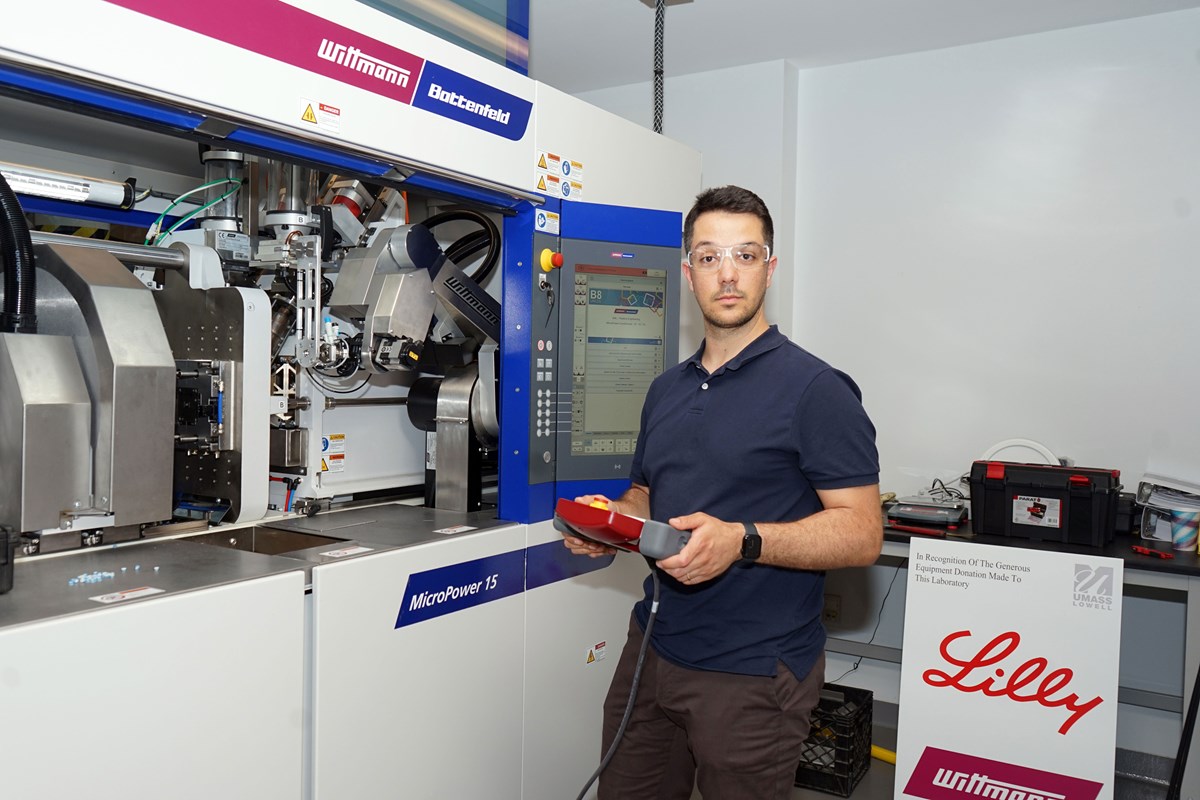
09/01/2024
By Ed Brennen
Davide Masato was a mechanical engineering Ph.D. student at the University of Padova in his native Italy when he first learned his way around a Wittmann Battenfeld micro injection molding machine.
When Masato joined UML’s Department of Plastics Engineering as an assistant professor in 2018, he discussed the possibility of acquiring one of the machines. But with a price tag pushing a half million dollars, it was simply out of reach.
Six years later, thanks to several alumni connections and Masato’s diligence, plastics engineering majors at UMass Lowell are being trained on the program’s first micro injection molding machine. The machine is also capable of overmolding, which combines multiple materials seamlessly into a single part or product.
“In some respects, it’s even more advanced than what students would find in industry when dealing with plastic micro parts,” Masato says while giving an overview of the equipment, which is installed at the Saab Emerging Technologies and Innovation Center on North Campus.
Indianapolis-based health care company Eli Lilly & Co., where plastics engineering alum Ho-Seon Jin ’92 is senior director of engineering, donated the machine to the university in April. Before it arrived, it was refurbished and upgraded by Wittmann USA in Torrington, Connecticut, from which mechanical engineering alum David Preusse ’85 recently retired as president.
Jin and Preusse joined Francis College of Engineering Dean James Sherwood and Masato for a ceremonial ribbon-cutting at UML. “UMass Lowell means a lot to me, and I hope this helps the university continue its great work to develop talented engineers for the plastics industry,” Jin said.
“UMass Lowell means a lot to me, and I hope this helps the university continue its great work to develop talented engineers for the plastics industry,” -Ho-Seon Jin ’92
UML had to compete with several other schools to receive the donation from Lilly, according to Masato, who spent nearly a year working with colleagues in crafting the university’s proposal, which included using the machine for manufacturing and materials research, undergraduate and graduate teaching, and outreach activities.
With the machine now installed, students will get hands-on experience with micro injection molding, which is used to make biomedical devices, electronics, sensors and more. Masato says it will also enable research on biomaterials that are used in medical applications.
Students will also learn about automation, as the machine is equipped with a robot that can pick the parts from the mold and move them over to quality control.
“That’s great, because when students go out in industry, they have to understand automation and the quality control that goes with that,” Masato says. “It’s good for them to see everything integrated in one machine.”
Masato has already integrated the machine into the curriculum. In August, he led a three-day Precision and Micro Injection Molding seminar with plastics engineering alum Vijay Kudchadkar ’06, who is director of innovation and business development for Nissha Medical Technologies (formerly Isometric Micro Molding).
Plastics engineering alumna Donna Bibber ’88 was vice president of corporate development at Isometric, where the machine was hosted for a Lilly project.
“A lot of alumni connections and their support to the department made this possible,” says Masato, who is “happy to establish the presence and relevance of precision and micro injection molding” at UMass Lowell.