Brooks Is the First Company to Sponsor an Industry Ph.D. Fellowship Program for Diversity
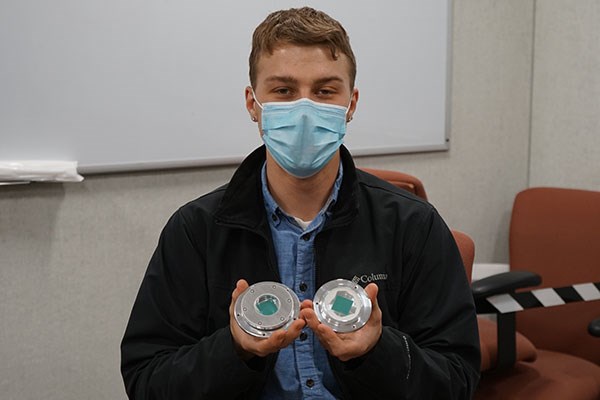
Jacob Fager ’21 displays the two cases for laser reflectors that his team designed for their senior industrial capstone project, one of three sponsored by Brooks Automation.
05/19/2021
By Katharine Webster
For seniors Stanley Leung and Shane Roy, the best part of their senior industrial capstone project — designing a test box for robots made by Brooks Automation — was getting practical experience that would help them transition to the working world.
For Teddy MacDonald, it was the challenge of understanding what Brooks, a Chelmsford, Massachusetts, company that makes automation systems used in high-tech manufacturing and life sciences, needed, and then figuring out the best way to design the test box while balancing costs and technical trade-offs.
For team leader Adam Quinn, it was working across disciplines with his group and consulting with the team’s Brooks Automation mentor, Richard Barrett ’78, ’81, and Asst. Teaching Prof. of Electrical and Computer Engineering Jean-Francois Millithaler as “resources.” And finally succeeding.
“We all embraced that you might fail sometimes and have some triumphs sometimes, but we were all doing this together,” Quinn says. “And it’s exciting to know that something we’ve put together will be part of these super-complex robots.”
Barrett, a software engineering manager at Brooks, is equally enthusiastic. He says he will be putting the student-designed test box to work right away because it will allow his quality assurance team to easily test the company’s LEAP robots — used worldwide by companies that manufacture silicon chips — in all three “personality” modes. Before, he could test only one mode.
“If we’d done this in-house, it probably would have taken longer,” Barrett says. “Throughout the whole project, the students have shown dedication and intelligence.”
Brooks’ semiconductor division, which makes robot, vacuum and automation systems for manufacturers of silicon chips, sponsors three industrial capstones every academic year. That’s the backbone of the company’s partnership with the Francis College of Engineering, a collaboration that has grown to include Brooks’ support for RAMP — a summer program for diverse first-year engineering students — and sponsorship of a campus laboratory, as well as internships. Brooks engineers and the company’s CEO, Steve Schwartz, serve on college and department advisory boards, and Brooks uses the university’s Core Research Facilities, too.
For the first time this fall, Brooks also will provide a fellowship to support a Ph.D. student for three years at $80,000 a year, says David Jarzynka, president of the company’s semiconductor solutions group. Brooks also loves to hire new graduates with bachelor’s and master’s degrees, he says.
“The most difficult thing is to get great talent, people with passion who are able to innovate,” Jarzynka says. “Our partnership with UMass Lowell is key to that.”
Sally Washburn, senior director of development for the Francis College of Engineering, says Brooks is always looking for new ways to partner with the university, both to help students and to invest in a pipeline of engineering talent for the Merrimack Valley. That is how the Brooks Fellowship idea arose: in mutual discussions about how to incentivize students to go on for a doctorate, when completing one usually takes five-plus years and engineering graduates can get jobs without an advanced degree. The Brooks Fellowship will allow a student to focus solely on their Ph.D. classes and research, she says.
“I’ve been impressed by Brooks’ corporate responsibility. It’s not just a one-way street to get the talent,” Washburn says. “They don’t wait for another company to do something and then follow. They come up with ideas, they try them, and they’re willing to take the risk.”
Much of the close relationship is due to the advocacy of Brooks’ systems engineering director, Leigh Sharrock ’03, an electrical engineering alumnus who championed having the company sponsor industrial capstone projects for seniors. For the past five years, Brooks has sponsored three industrial capstones for teams of mechanical, electrical, plastics and computer engineering students — and engineers at Brooks compete to come up with projects for them, Sharrock says.
“We focus on creative problems that we might not have the time or the resources to resolve and that are also within the boundaries of what the students can achieve in a few months,” he says. “The students often bring a different perspective to what we’ve been thinking about for a good while, and they get a lot of experience. I wish we’d had this when I was graduating.”
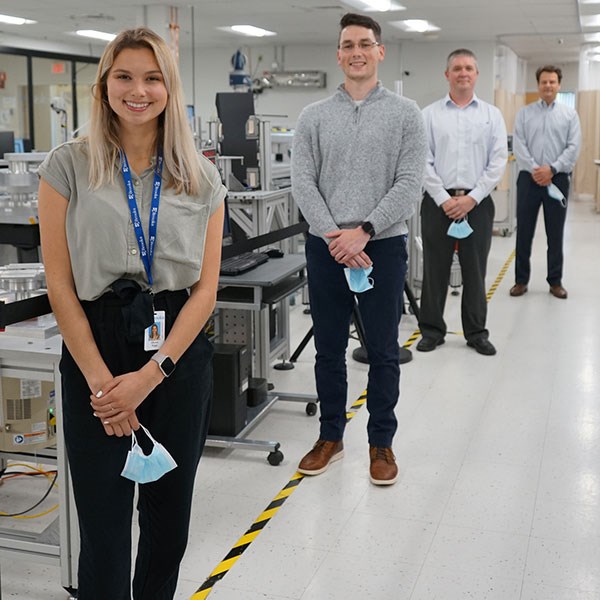
Mechanical engineers Allyson Toppi ’20, ’21 and Kevin Twitchell ’14, ’20 with Systems Engineering Director Leigh Sharrock ’03 and Vice President Alex Krupyshev in Brooks Automation’s robotics reliability lab.
Jacob Fager ’21, a mechanical engineering graduate, is now working for National Grid as an assistant field supervisor for gas pipeline installation and maintenance. Fager chose a two-semester Brooks industrial capstone instead of a one-semester academic capstone because “the company project seemed a whole lot more relevant and exciting.”
Fager took the lead for a team charged with figuring out how to put special laser reflectors inside the vacuum transport systems where silicon chips are manufactured, while protecting the reflectors from high heat. He says he also learned “soft” skills like project management, as well as how to collaborate and adapt under pandemic-imposed conditions, such as being unable to visit Brooks or use their facilities to test the two reflector cases his team had developed.
“As engineers, we want to see things and touch them and turn them sideways, and we couldn’t do that. But Brooks did a great job of giving us the tools we needed so we could work independently,” he says, noting that the team’s industry mentor provided them with reflectors, lasers and laser sensors. The team used university labs for strength and high heat testing.
Brooks also hires a lot of student interns and then tries to employ those who do well. Mechanical engineer Allyson Toppi ’20, ’21 got an internship at Brooks the summer before her junior year. She tested the thin, metal bands that move the robots’ arms, and even invented a device to test the tension without dismantling the arms.
Toppi says that her supervisor, Joe Hallisey, treated her like an engineer from Day One, and when she did her final presentation, many people told her how valuable her work was to the company.
“Even though I was an intern, I felt like a real engineer there,” she says.
She was invited back for a second summer internship and then kept on part-time as she pursued a master’s degree, with Hallisey’s encouragement. Now, Brooks has hired her full-time into its 18-month rotational program for new engineers.
Toppi joins the 50-plus UMass Lowell alumni who already work there, including mechanical engineer Kevin Twitchell ’14, ’20. Twitchell also started at Brooks as a summer intern in the automation mechanical engineering and robotics groups, where he put together documentation for new employees and built a LEAP robot from the ground up.
He continued to work full-time in robot testing and design at Brooks while finishing his bachelor’s degree in mechanical engineering technology at night. Now, he is starting his third, six-month rotation as an engineer, and he is planning to make his career at the company.
“It’s a great job. They’ve given me this great opportunity, so I’ve tried to show my worth,” Twitchell says. “I’ll be here for the long haul.”